Titanium alloy has a series of advantages such as excellent corrosion resistance, low density, high specific strength, and good high-temperature performance. It is an emerging structural material and functional material and is currently widely used in aerospace, petrochemicals, shipbuilding, automobiles, medicine, etc. Department Among the conventional product types of titanium alloys, plates are the largest one, accounting for about 56% of the titanium market. In terms of requirements for the board, it is required that the chemical composition is stable, no segregation, the structure is refined and uniform, the performance is stable, the surface is smooth, beautiful, and defect-free, etc. The main quality problem of cold-rolled plates, which account for half of titanium alloy plates, is surface defects.
Due to the long production process and thin specifications of cold-rolled titanium plates, defects such as linear defects, holes, inclusions, peeling, and bubbles are prone to occur. Statistics show that surface defects mainly include metal and non-metal intrusions, holes, mechanical damage, surface cracks, oil stains and peeling. Therefore, it is necessary to analyze the causes of surface defects of cold-rolled plates, and then find out corresponding prevention methods to reduce or eliminate surface defects and improve the quality of cold-rolled plate products.
1. Common defects and causes
1.1 Inclusion defects
For cold-rolled titanium plates, the most common problem of intrusion is shown in Figure 1. The edge burrs and surface foreign matter of the titanium plate are pressed into the surface of the product. If the foreign matter is not dealt with during the production process of the cold-rolled plate, it may cause quality problems and reduce the performance of the cold-rolled plate.
It will also cause the appearance to not meet the standards, and the intrusion of foreign matter will cause uneven color. Under the premise of the current high standard precision requirements, the products produced cannot meet this standard. Therefore, the edge burrs and surface foreign matter of the slab should be removed promptly to ensure civilized production.
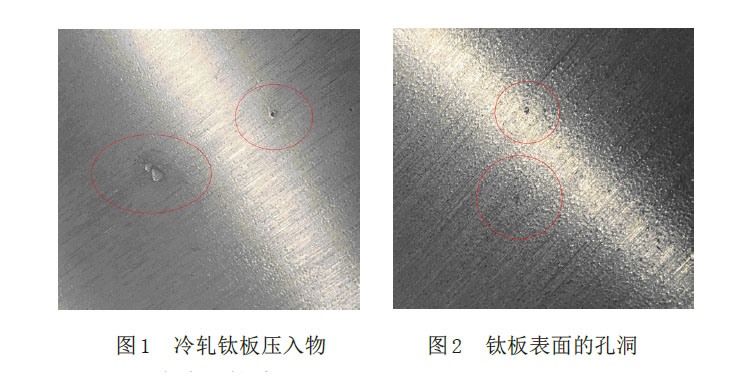
1.2 Surface defects such as potholes
Potholes are a common surface defect in thin titanium plates. The holes on the surface of the titanium plate are shown in Figure 2 and Figure 3. Most of the holes can only be formed after cold rolling, and a small part of the hot-rolled surface has already formed holes. In pit defects, abnormal structures are generally visible, and inclusions may also appear. If the oxide scale is not removed during pickling, or the rolling environment is not clean, dirt adheres to the surface, or the rolls are not ground in time, they will be pressed into the thin slab to form defects during rolling. The pit defect appears in a local area of one of the rolling surfaces of the plate. Sometimes a titanium plate has 1 to 2 defects visible to the naked eye, and in severe cases there can be 5 to 6 defects. The defective surface area has dense pits in a honeycomb shape and has lost its original metallic luster.
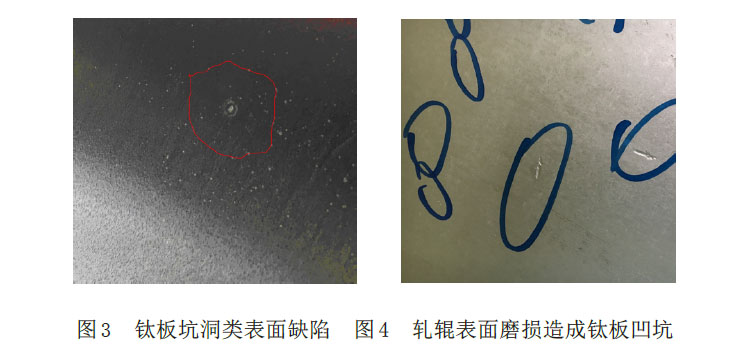
1.3 Mechanical damage defects
Scratches, roller marks, and creasing are relatively common mechanical damage defects. Their appearance is characterized by indentations and scratches, with different shapes and sizes. Scratches occur when the guide plate, roller table and tools are not clean, there are angular burrs, etc. (as shown in Figure 5), and the surface is scratched during rolling. If the scratch problem is not carefully checked, the stamping of the parts in subsequent production will cause cracks. If the scratch area is large and the depth is relatively deep, it will directly lead to the scrapping of the parts. For example, the appearance of roller marks or continuous convex shapes on the titanium plate, as well as folding dents, will cause quality problems on the titanium plate (Figure 6). The occurrence of the above problems is related to the wear of the roll surface. Severe wear and pressure on the plate corners will cause pits on the roll, as shown in Figure 4).
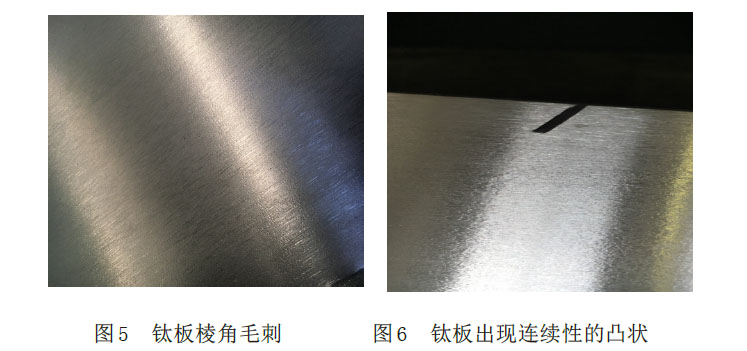
1.4 Surface crack defects
Surface crack defect is a common surface defect in titanium plates. It is mainly caused by the cracked edge of the incoming material that has not been removed and expands during rolling. The cracks are densely distributed along the rolling direction, but discontinuous, and their shape is long strip-shaped cracks of different lengths and thicknesses (Figure 7 and Figure 8). The cold rolling processing rate is too large, and the edges are pulled apart during rolling. The titanium plate is uneven during annealing, which easily causes uneven surface deformation. As this deformation accumulates in the same pass, it will eventually lead to edge cracks. Unreasonable roll curve configuration can also cause edge cracks.
Figure 7: Long cracks appear on the surface of the titanium plate. Figure 8: There are cracks of different lengths and thickness on the surface of the titanium plate. Check the incoming materials. Materials with cracked edges must be removed in time. During the rolling process, the procedures must be adjusted. , master the roll curve, and continuously improve the annealing process. Strictly control the quality of raw materials. The quality of the alloy must be ensured for the raw materials selected. Sufficient time must be ensured when alkaline pickling is performed after annealing. Quality problems such as holes on the surface must be removed in a timely manner. , guaranteed to be clean and free of quality defects.
1.5 Surface peeling defects
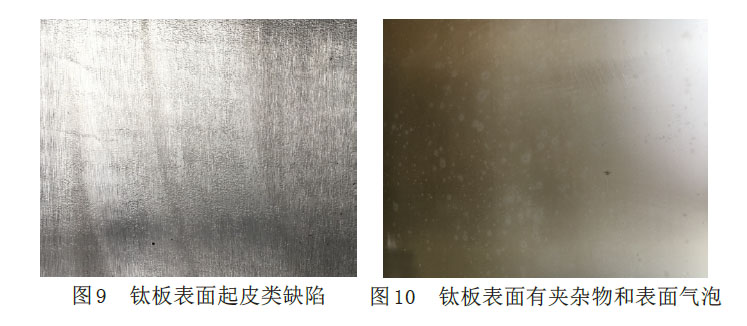
The main cause of surface peeling defects is that the surface of the titanium plate is affected by inclusions and surface bubbles. The pass processing rate is small and there are too many rolling passes. During the rolling process of the titanium plate, surface peeling defects are finally formed after pressing. (As shown in Figure 9 Figure 10).
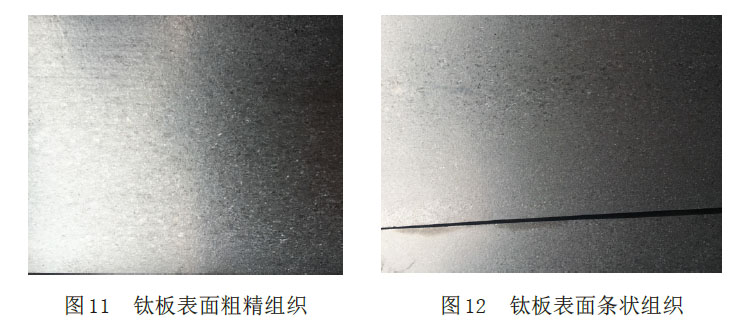
2. Effective control measures to prevent surface defects
2.1 Optimize melting and strengthen equipment management
In the process of cold-rolling titanium plates, process parameters are very important, so the parameters must be optimized to make the material structure more uniform, and the power density must also be strictly controlled to ensure that the titanium melt remains on the hearth for a longer period of time. If the standard is reached, the alloy elements can be more uniform and segregation problems can be eliminated.
The work roll can be repaired in time for slight small-area indentations, and the work roll can be replaced for serious indentations. According to the changes in rolling specifications, the rolls can be adjusted in time to improve the cooling of the rolls and reduce the uneven deformation of the titanium plate.
① Observe frequently and change rolls frequently. If the pressing is weak, the diameter of the roll is small, and the wear is uneven, the roll should be replaced in time
② Check the incoming materials carefully and strictly implement the intermediate billet standards. If it is found that the transverse plate difference of the incoming materials is large, “mountain” “Defects such as shaped iron should be sorted in time and produced separately
③ Try to use clean mechanical oil as lubricant. If the roll temperature is too high, you can also mix oil and water for rolling, but avoid uneven plate and roll temperatures.
④ Thicken both sides of the work roll bearing box to increase the thickness of the slide plate to prevent cross-talk
⑤ Reasonably distribute the pressure (the principle of gradually reducing the amount of pressure with each pass) to make it deform evenly. The above measures basically solve the shape problem of pure titanium cold-rolled plates.
2.2 Strengthen the management of blanks
Strict billet quality inspection is required to ensure the thickness accuracy of hot-rolled raw materials. Seriously over-thick or ultra-thin parts should be removed. Defects are cleaned up in time, and unqualified billets are not put into production; the throwing speed of rolling is controlled, and the appropriate reduction is maintained to keep the lower stress consistent with the system.
2.3 Strengthen management between processes
When entering the process room, personnel need to change work clothes, wear protective shoes, and wear shoe covers, keep the process room clean and tidy to the greatest extent, clean the process room in a timely manner, and clean the rolls before production to ensure that the rolls are bright and defect-free.
2.4 Clean up oil stains promptly to prevent stains and defects
Avoid unit oil leakage, improve the quality of various solutions (turbine oil, transformer oil, rolling oil, cotton oil, sesame oil, palm oil), avoid abnormal shutdown of belt material, and effectively control track defects.
There are many reasons for poor alkali pickling. Problems in production details will lead to poor alkali pickling. They are mainly divided into poor pickling and excessive pickling. This will again affect the hardness and thickness of the cold-oxygen plate. To solve the problem of poor pickling, the main thing is to control the quality and production process of the cold-rolled plate. Whether it is specifications or temperature, it must be reasonable, and the process must be strictly followed. It is necessary to check the quality of materials and remove magazines in time to improve the quality of finished products.